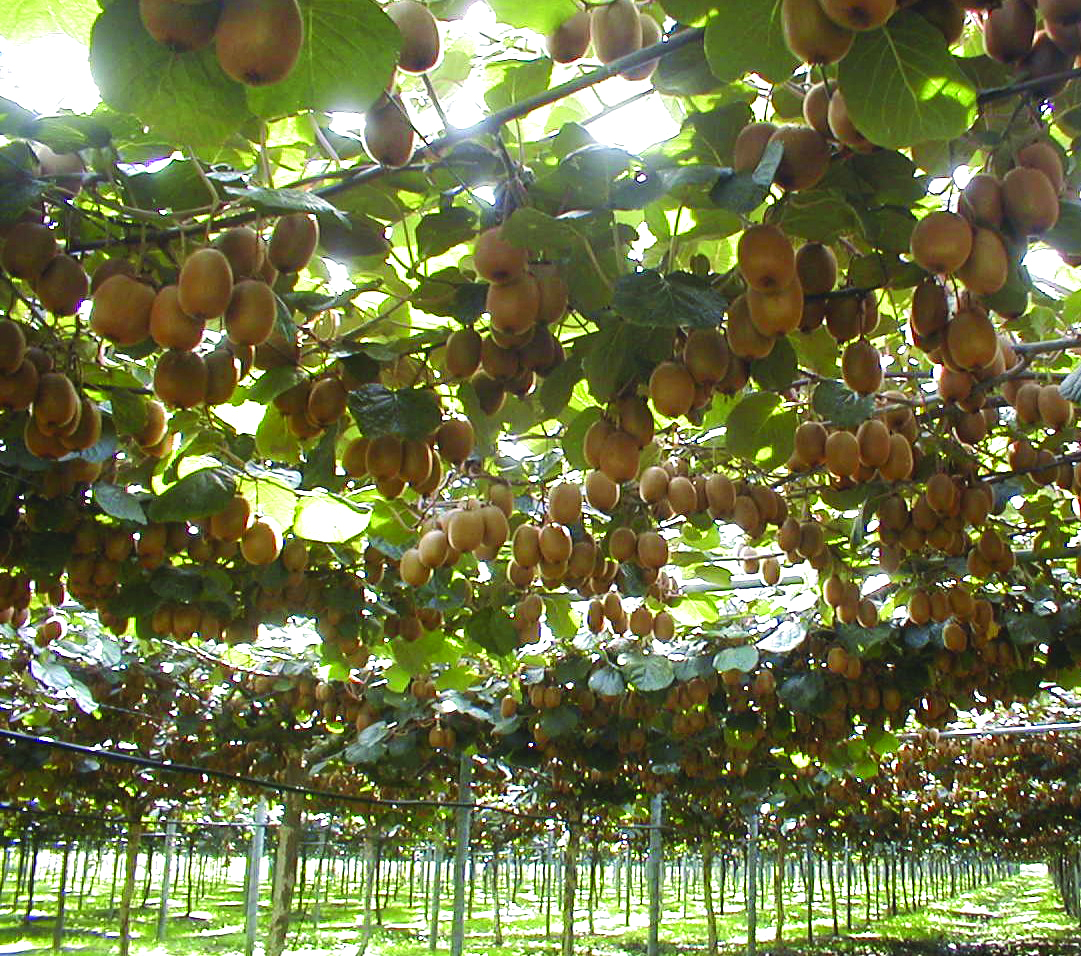
Mazzoni company is a leader in the agro-food industry and for over 60 years stands out on the Italian and foreign markets for the constant and perpetual analysis of the consumer needs that are more and more inclined to the consumption of “natural products”, in recent years. By the end the concept of sustainability is accompanying and will accompany more and more commercial strategies within Mazzoni group with the goal of always offering quality and healthy products, cultivated on its territory and in suitable areas, while respecting and protecting the environment. Mazzoni has been able to capitalize on all these aspects aware of the best practices of energy conservation, proper waste management and the rational use of water. Dynamism and experience in this trade enabled a perfect combination of the concept of sustainability and business practices. “For those who do not share the crop experience and and are not used to visit Mazzoni warehouses and packing houses cannot perceive the huge investments in technology and human resources for the protection of sustainable agriculture, during the last 15 years” declares Sergio Trevisan import-export top manager. Nursery research managed by the company focused on fruit and vegetable species, no OGM, which require a low use of chemical interventions, thus reducing the environmental and the food chain impact. The farms within the Mazzoni group work in respect of the integrated production procedures which combine the best university knowledge and experimental experience of technical experts in the field who apply organic farming practices, whenever possible. Photovoltaic systems were installed to produce clean energy for conditioning and refrigerating operations. Storage systems are the latest generation and in the cells is possible to create a controlled and/or dynamic atmosphere which guarantee maximum conservation, food safety and shelf life of the products. Also, Mazzoni preserves the workers’rights through suitable, healthy and safe work environment with respect of the legislation on prevention and safety in the workplace. MV